Plastic extrusion for thermoplastics, PVC, and engineering plastics
Plastic extrusion for thermoplastics, PVC, and engineering plastics
Blog Article
Understanding the Basics and Applications of Plastic Extrusion in Modern Production
In the realm of contemporary manufacturing, the strategy of plastic extrusion plays a crucial role - plastic extrusion. This elaborate procedure, including the melting and shaping of plastic via specialized passes away, is leveraged across numerous markets for the creation of diverse products. From automobile components to durable goods product packaging, the applications are large, and the capacity for sustainability is similarly outstanding. Untangling the basics of this procedure discloses the real adaptability and potential of plastic extrusion.
The Fundamentals of Plastic Extrusion Process
While it might show up complex, the fundamentals of the plastic extrusion process are based upon fairly straightforward concepts. It is a production procedure where plastic is thawed and after that formed into a continual account through a die. The raw plastic product, commonly in the form of pellets, is fed right into an extruder. Inside the extruder, the plastic goes through heat and pressure, triggering it to thaw. The molten plastic is after that required with a designed opening, called a die, to create a long, continual item. The extruded item is cooled down and afterwards cut to the preferred length. The plastic extrusion process is extensively used in various industries due to its cost-effectiveness, efficiency, and versatility.
Various Types of Plastic Extrusion Methods
Structure upon the basic understanding of the plastic extrusion process, it is necessary to explore the numerous strategies entailed in this production technique. In contrast, sheet extrusion creates huge, level sheets of plastic, which are normally further processed right into items such as food product packaging, shower curtains, and automobile parts. Recognizing these strategies is key to utilizing plastic extrusion effectively in contemporary production.
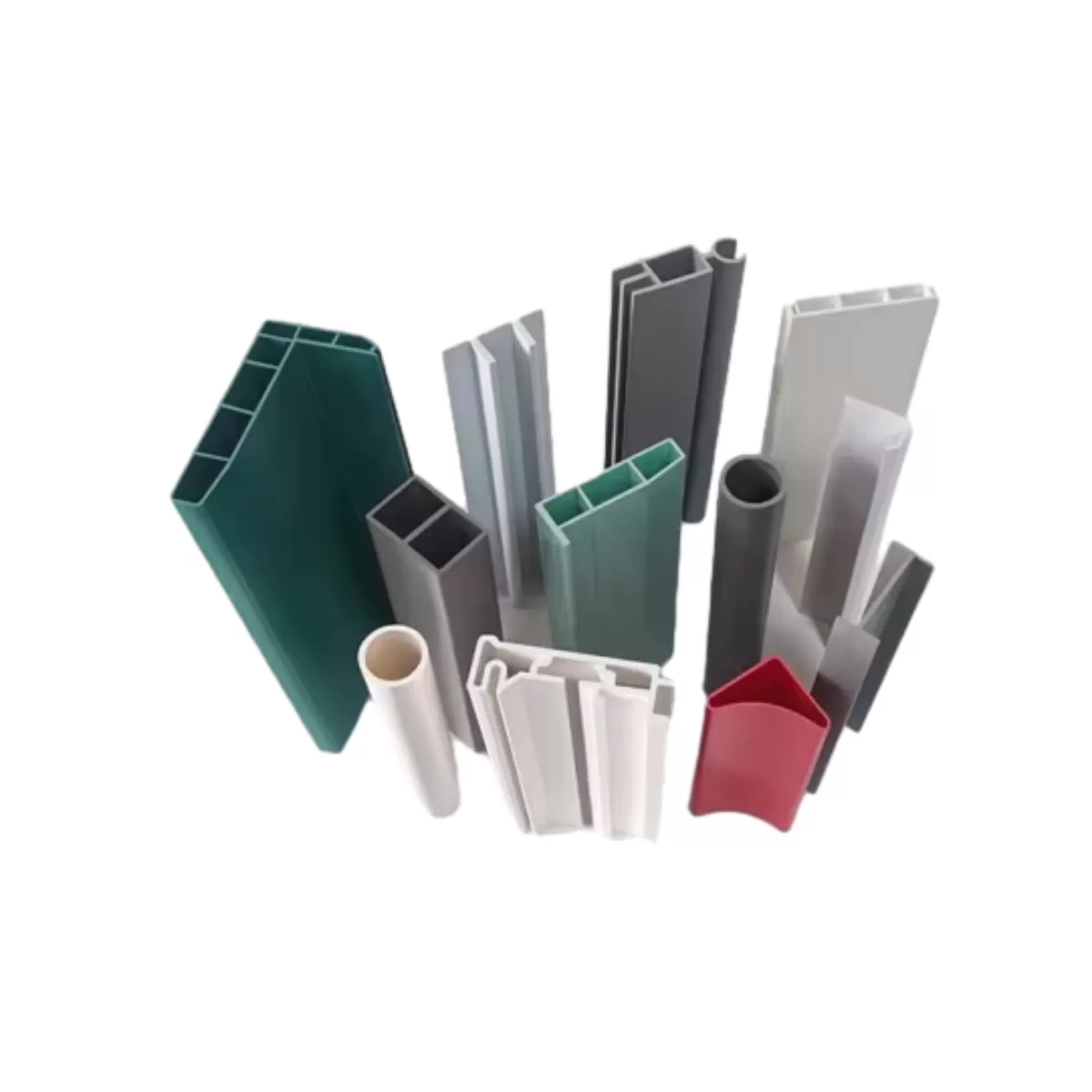
The Role of Plastic Extrusion in the Automotive Sector
An overwhelming bulk of components in modern cars are items of the plastic extrusion process. This procedure has actually transformed the automobile sector, transforming it into a more efficient, economical, and adaptable production market. Plastic extrusion is mostly utilized in the manufacturing of numerous vehicle components such as bumpers, grills, door panels, and dashboard trim. The procedure offers an attire, consistent result, allowing suppliers to produce high-volume components with wonderful precision and marginal waste. The lightness of the extruded plastic parts adds to the overall decrease in vehicle weight, enhancing gas effectiveness. Additionally, the sturdiness and resistance of these components to warmth, chilly, and influence improve the durability of automobiles. Therefore, plastic extrusion plays a pivotal function in automobile production.
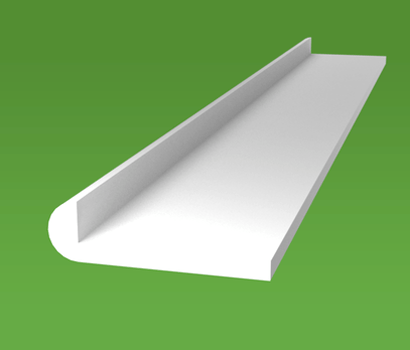
Applications of Plastic Extrusion in Customer Product Manufacturing
Past its considerable effect on look at this web-site the automobile market, plastic extrusion shows equally effective in the realm of durable goods making. This process is critical in creating a large selection of products, from food product packaging to home home appliances, toys, and also clinical gadgets. The versatility of plastic extrusion permits manufacturers to develop and generate complicated forms and sizes with high accuracy and effectiveness. Due to the recyclability of many plastics, squeezed out parts can be reprocessed, lowering waste and cost (plastic extrusion). The flexibility, flexibility, and cost-effectiveness of plastic extrusion make it a recommended choice for many durable goods manufacturers, adding considerably to the sector's growth and development. The environmental effects of this read the article extensive use require mindful consideration, a topic to be reviewed even more in the subsequent section.
Environmental Impact and Sustainability in Plastic Extrusion
The prevalent use of plastic extrusion in producing welcomes examination of its eco-friendly ramifications. As a process that frequently uses non-biodegradable products, the ecological effect can be considerable. Power consumption, waste manufacturing, and carbon discharges are all concerns. Sector improvements are raising sustainability. Effective equipment reduces power use, while waste management systems recycle scrap plastic, reducing raw product demands. Additionally, the advancement of biodegradable plastics supplies an extra eco-friendly alternative. In spite of these renovations, even more advancement is required to mitigate the ecological impact of plastic extrusion. As society leans towards sustainability, makers must adjust to remain viable, emphasizing the relevance of continuous research study and innovation in this field.
Conclusion
In conclusion, get more plastic extrusion plays an important role in modern production, especially in the vehicle and customer items markets. Recognizing the fundamentals of this process is key to optimizing its benefits and applications.
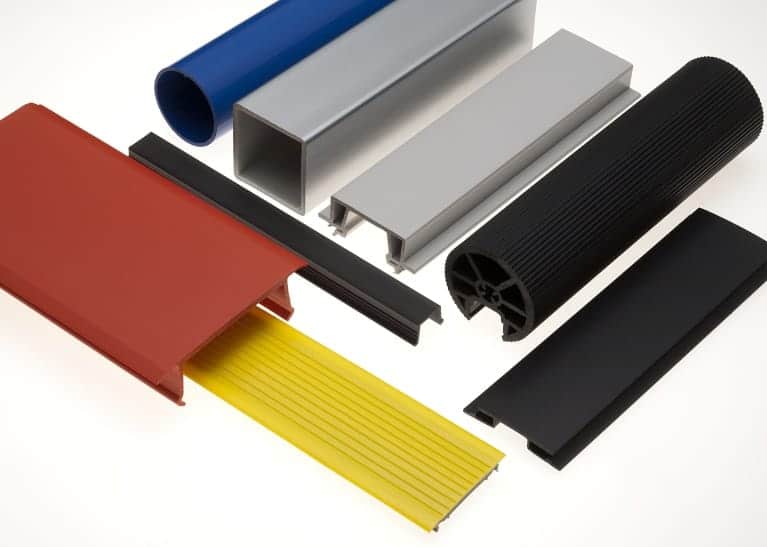
The plastic extrusion process is thoroughly utilized in numerous sectors due to its versatility, performance, and cost-effectiveness.
Building upon the fundamental understanding of the plastic extrusion process, it is needed to explore the various techniques included in this production technique. plastic extrusion. In comparison, sheet extrusion produces huge, level sheets of plastic, which are typically additional processed right into items such as food packaging, shower drapes, and car components.A frustrating majority of components in modern cars are items of the plastic extrusion process
Report this page